Semi Automatic Block Machine – QT4-24 Model
QT4-24 Semi Automatic Brick Making Machine
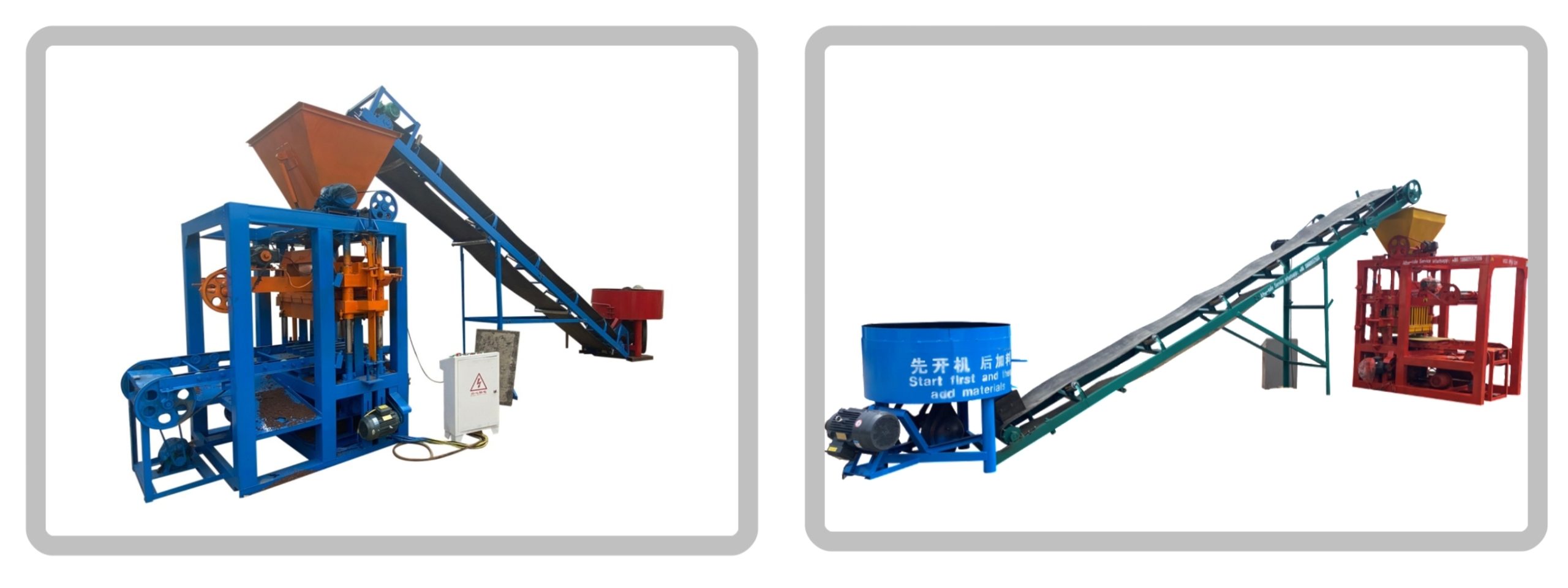
(1). Breif Introduction of QT4-24 Brick Making Machine:
The QT4-24 semi-automatic brick production line mainly includes the following parts: mixer, conveyor, brick making machine, brick discharging platform, manual cart. The entire production line requires 4 workers to operate, and the operating area requires 60 square meters. The factory area takes into account the raw material placement area, machine placement area, finished product area, drying area, etc., and requires about 600 square meters. QT4-24 can produce bricks of different sizes and types, such as hollow bricks, paving bricks, curbstones, solid bricks, square bricks, etc. The following information for QT4-24 hollow block machine is theoretically for reference, it will be a little different vary from different clients as per their real production condition.Land area | 600 Square Meters | Water Consumption | 2.5 T/day |
Workshop area | 60 Square Meters | Electricity Voltage &Frequency | 220V/380V/415V;50HZ/60HZ |
Labors Quantity | 4 workers | Power Consumption | 22.45KW*8 Hours=179.6 KWH; |
Cement Consumption | 7.3Tons per day | Sand consumption | 29.2 tons per day |
Crushed stones consumption | 36.5 tons per day |
(2). Working Process of QT4-24 Brick Pressing Machine:
- First, a worker needs to feed the material into the mixer manually. The mixer model is JQ350, Input capacity:500L, output capacity: 350L. The bottom plate thickness is 7mm, the barrel wall thickness is 8mm, and the barrel height is 50cm. The motor power is 7.5kw, the mixer size is 1.2*1.2*1.5m. The weight is 350kg. The mixing cycle is about 60 seconds. There is an electric control cabinet to control the mixer and the conveyor belt. To reduce the wear on the barrel wall, an additional protective layer can be added to the barrel wall. There are three solid mixing arms, and the mixing blades on the mixing arm heads can be replaced. To save manpower, customers can choose to dig a pit and put the mixer into the pit, or build a small platform to feed the mixer horizontally.
- After the materials are fully stirred, they are sent to the hopper above the brick making machine through a 6m long conveyor. The conveyor belt width is 550mm, the motor power is 1.5KW, and the weight is 550KG. The belt is a V-shaped rubber belt, which can increase friction when conveying materials and prevent materials from slipping. The transmission method is through a pulley, which reduces speed and has low cost. The V-belt needs to be replaced regularly.
- After the material enters the hopper above the brick making machine, a worker operates the electric control cabinet to control the brick making machine to unload the material. Then use the equipped small shovel to manually spread the material, manually place the board, and then operate the electric control cabinet to make bricks. The up and down movement of the beam drives the material cart to move forward and backward, and at the same time completes the work of adding materials and pushing bricks. When the beam is raised, the main shaft cam pushes the pressing head body to push the pressed product out of the mold cavity. The material cart moves at the same time to push the ejected molded product through the mold cavity to the brick discharge platform. The workers then use carts to transport the bricks to the drying area. It takes a week to dry naturally, and the bricks are watered 2-3 times a week. The power of QT4-24 is 13.25KW, the size is: 1.8*1.5*2.52m. The exciting force is 50Kn, equipped with JZQ250 reducer, and the weight is 1500KG. The unloading motor is 0.75KW, the upper mold vibration motor is 2.2KW, the lower mold vibration motor is 3KW*2, the mold lifting motor is 2.2kw, the upper push-pull mold motor is 0.75kw, and the brick platform motor is 0.75kw. QT4-24 uses a vibration table to make the block mold more evenly. stressed; the electrical panel is more advanced, and the semi-automatic operating system is adopted, which is easy to operate.
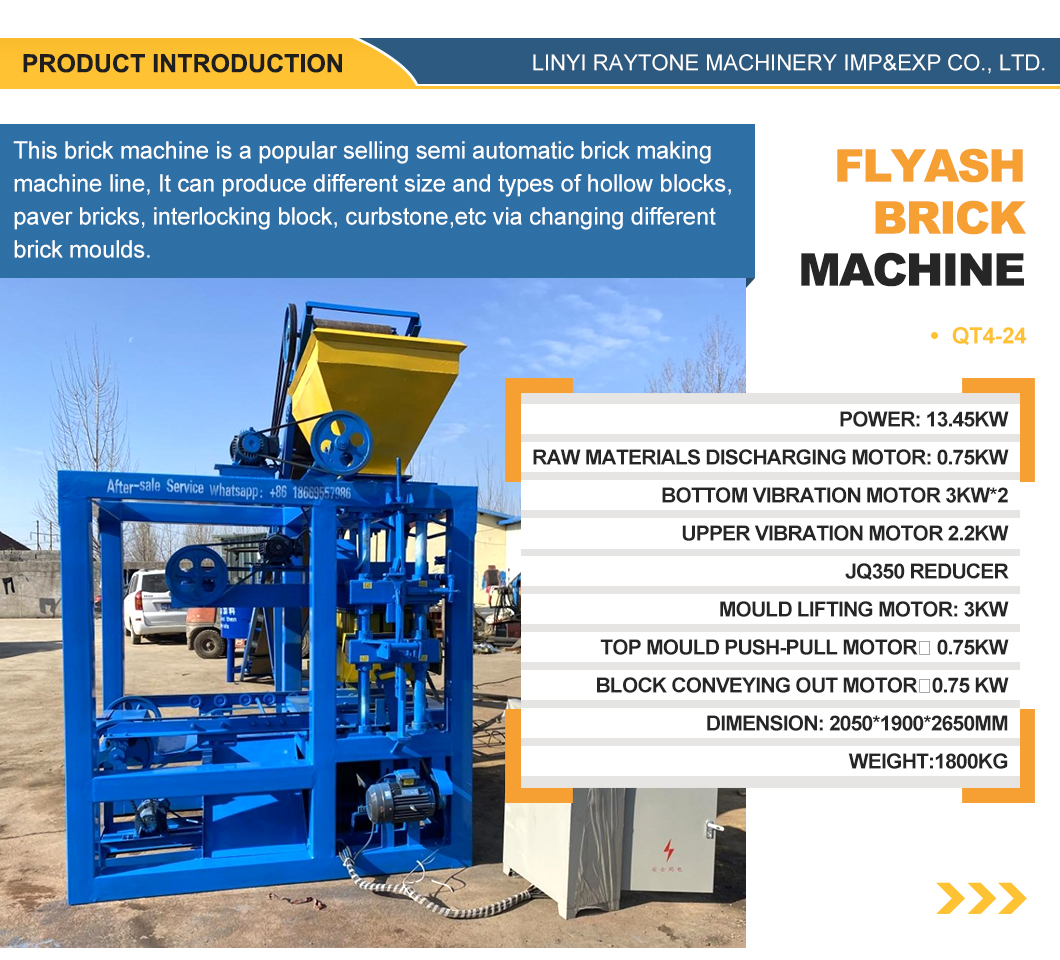
(3). Theoretical Capacity of QT4-24 Block Machine:
(4). Specific Parameters of Each Product in QT4-24 Block Machine:
No. | Item | Specifications | Photo | Unit | Qty |
1 | JQ350 Concrete mixer | Input Capacity 500L Output Capacity 350L Motor Power 7.5KW Diameter 1.2M Size 1.2*1.2*1.4 M Weight 350KG Bottom plate Thickness: 7mm Barrel Thickness: 8mm Barrel Height: 50cmwith electric cabinet to control mixer and belt conveying machine | ![]() |
set | 1 |
Belt Conveying machine | Belt Conveying Length 6M Motor Power 1.5KW Belt Width 500mm Weight 550KGwith materials receiving hopper; electric motor with cycloidal pin gear speed reducer | ![]() |
set | 1 | |
2 | QT4-24 Host block making machine (Inc : Electric cabinet) | Shed or workshop area 60 square meters Factory area 600 square meters Labor quantity 4 Machine power 13.25kw Vibration force 50kn Reducer model: JZQ250 Diesel Generator Capacity: 30KVA Machine size: 1800*1500*2520mm Machine weight: 1500kg | ![]() |
set | 1 |
(5). Why Choose QT4-24 Semi Automatic Block Machine?
- QT4-24 block machine is one of our newly designed block making machine. With less power.
- It adopts full automatic spiral material laying method, so the material in the mould is well-distributed. With simple operation and high productivity, when producing hollow blocks, it has an advantage over the large hydraulic block machines.
- It is equipped with JQ350 speed reducer to raise and lower the mold, so it greatly increases the usage life of the speed reducer.
- It combines pressure and super vibration. The unloading motor is 0.75KW, the upper mold vibration motor is 2.2KW, the lower mold vibration motor is 3KW*2, the mold lifting motor is 2.2kw, the upper push-pull mold motor is 0.75kw, and the brick platform motor is 0.75kw, so the blocks made by this machine has high strength and accurate size.Its performance and product quality are comparable to the large equipment.
- About our mould: 900 degrees celsius high temperature heat treatment carburizing heat treatment makes the mould much more strong and durability, longer life.Cutting uses wire cutting to make the mold standard in shape and accurate in size. After heat treatment and carburizing technology, the rigid molecular structure is changed, the strength and hardness are increased, and it is more wear-resistant. After positioning processing and milling machine technology, the surface of the mold is smooth and smooth, and the dimensions are more accurate. The mould can be used around 100 thousand times.

(6). The blocks made from QT4-24 Brick Moulding Machine:
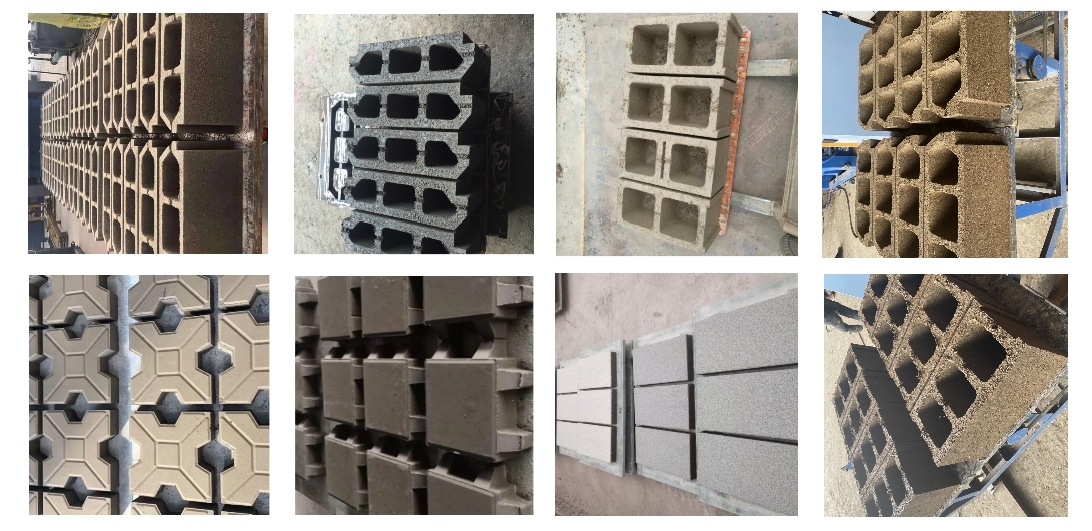
(7) How to Package and Transport Block Machine?
We can package the machines according to your requirements. Whether it’s a plywood box or an iron frame, we can use either. Each machine will be wrapped in plastic film to reduce wear and tear. Our on-time delivery rate is 100%.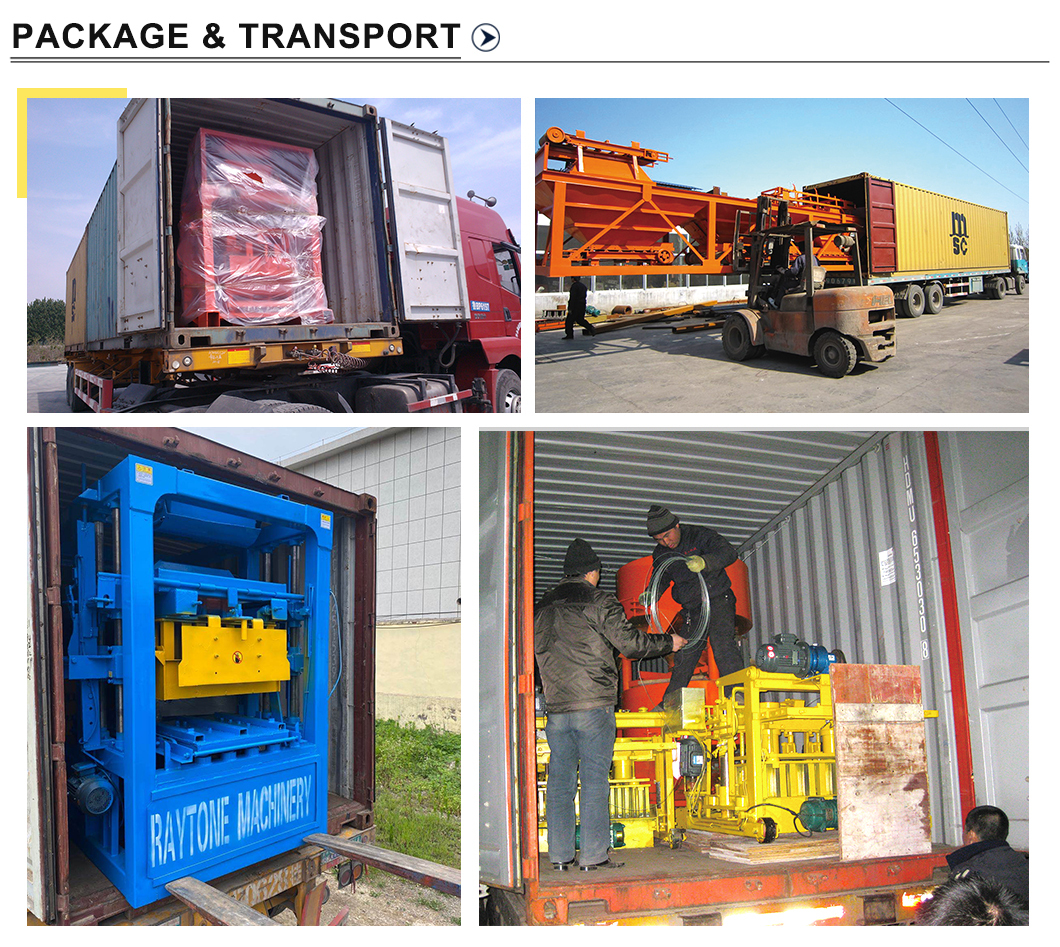
For more information, contact us!