Automatic Cement Block Machine QT4-25 Model
QT4-25 automatic block machine is a mechanical driven concrete block making machine, it can makes all the hollow blocks, paver bricks, interlocking blocks, curbstones etc,
but because it is not equipped with pigments feeding machine, so it can not make paver bricks with color.
QT4-25 automatic cement block making machine can make 4 pieces of 8 inch hollow blocks per mould. Every mould cycle is 25 seconds.
QT4-25 automatic cement block machine is using 880*550*22mm GMT brick pallet.QT4-25 block machine can make 4608 piece of 8 inch hollow blocks per day.
Working Principle: The raw materials are proportionally added to the blender. Usually, water and cement bags are added first, followed by sand, stones and other raw materials.
As the mixing arm rotates, the mixing blades stir and mix the raw materials to form a uniform concrete slurry.
(2) Belt Conveyor Machine
Working Principle: The working principle of the V-shaped belt conveyor is to achieve rapid, efficient and stable material transportation through the inclined conveyor belt and the force of gravity.
The specific process includes: Power transmission: The motor transmits power through a reducer to the driving drum. The friction between the drum and the belt causes the belt to start moving.
Belt circulation: The belt loops around the driving drum, the reversing drum, and the tensioning drum to form a closed loop. It remains stable and operates under the support of the idler rollers.
(3) QT4-25 Host brick Machine
Working Principle: The main motor drives the reducer to rotate through the belt on the pulley, and then transmits the power to the small gear shaft through the coupling. The small gear drives the large gear to rotate (that is, the main shaft rotates). The crank connecting rod mechanism converts the circular motion into the up-and-down linear motion of the beam. The up-and-down movement of the beam drives the material cart to move forward and backward, and at the same time, it completes the feeding and brick pushing tasks. When the beam is lifted, the main shaft cam pushes the lower pressing head body, and the pressed-formed products are pushed out of the mold cavity. At the same time, the material cart acts, pushing the pushed-out formed products over the mold cavity opening to the picking platform and supplying the mold cavity material. The pressing system performs: feeding, pressing, removing from the mold cavity, pushing out the products, feeding… and the cycle of repetitive work repeats continuously.
(4) Single Row Block Stacking machine
Working Principle: The working principle of the brick stacking machine mainly consists of three parts: mechanical transmission, program control, and sensor detection. The mechanical transmission part is composed of motors, reducers, chains, etc., which are responsible for transmitting the power from the motor to various parts of the stacking machine. The program control part is the “brain” of the stacking machine. It controls the actions of the mechanical transmission through preset programs to achieve functions such as material grasping, movement, and stacking. The sensor detection part is the “eyes” of the stacking machine. It uses sensors such as photoelectric and limit switches to detect the position and posture of the materials, providing a basis for program control.
(5) GMT brick pallet
GMT(Glass Mat reinforced Thermoplastics), or glass fiber mat reinforced thermoplastic composite material, which is made of glass fiber as reinforcing material and thermoplastic resin as base material made by method of heating and pressurizing. The pressing process is made by the 3000 Ton pressure machines. Its density is 1200kg/cubic meters; its life can be 8 years, some can reach 10 years; now it is the most widely used among these brick pallets because cheaper cost and environmental, longer life, water-resistant, temperature resistance, less weight, can not be replaced by traditional pallets
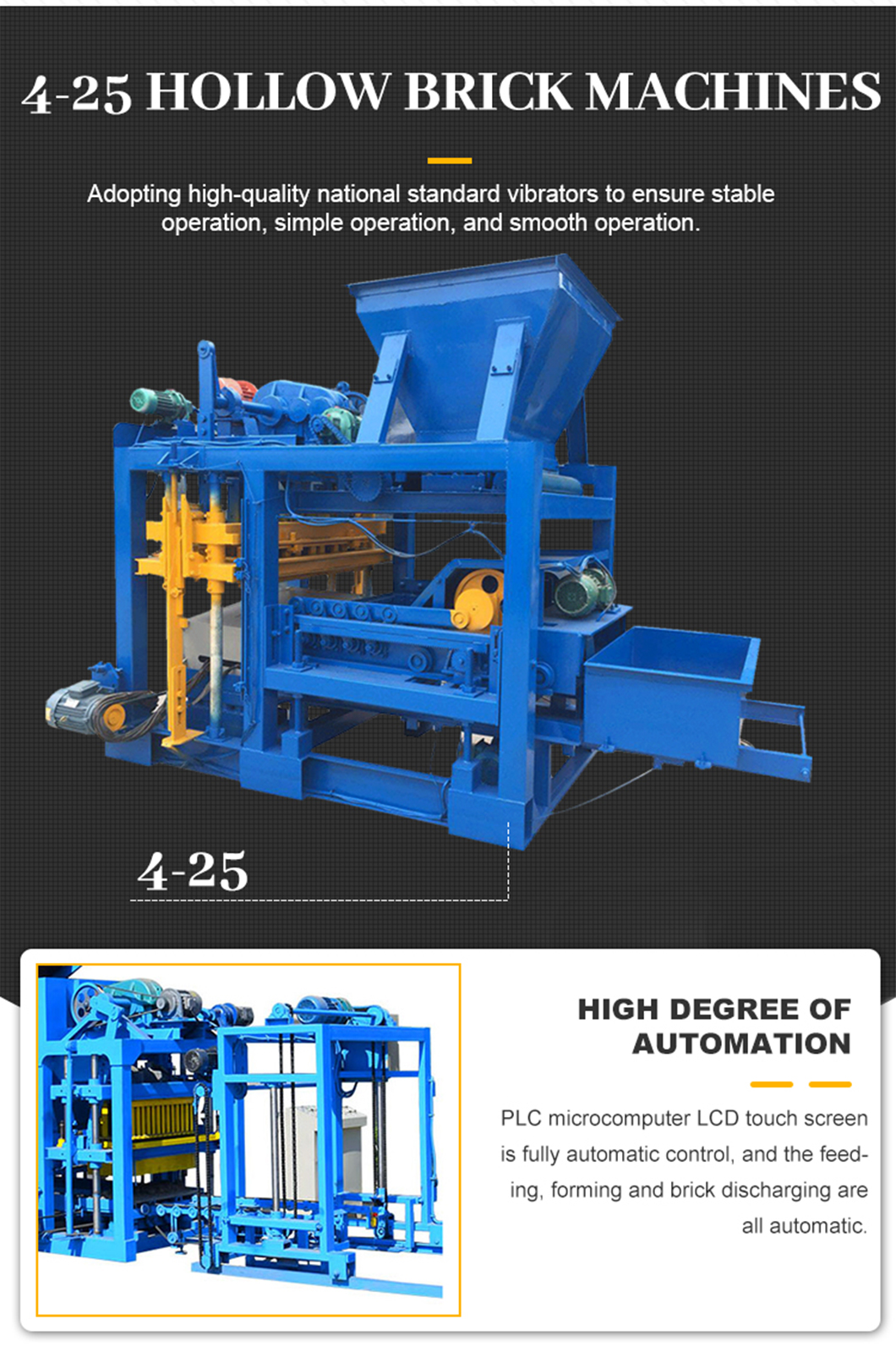
2. QT4-25 Automatic cement Block Machine line Basic Requirements for brick plant starting.
Land area | 1000 SQM | Water Consumption | 2.88 T/day |
Workshop area | 60 SQM | Electricity Voltage &Frequency | 220V/380V/415V; 50HZ/60HZ |
Labors | 6 workers | Power Consumption | 34.8KW*8 Hours= 278.4KWH; |
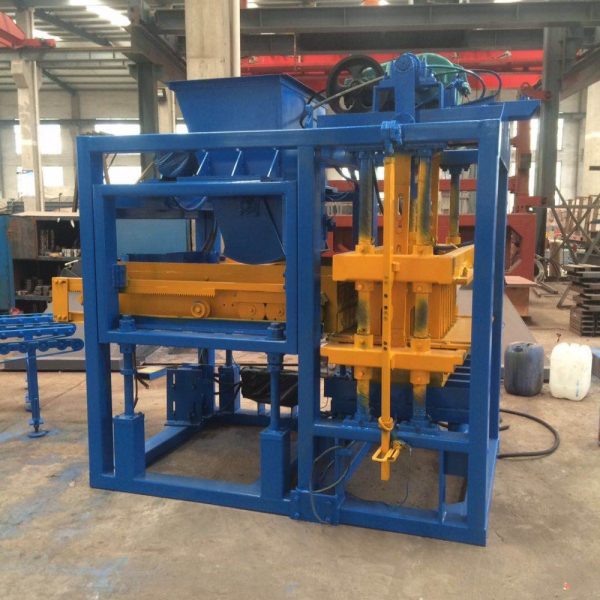
Detailed introduction of each single machine from QT4-25 automatic cement block machine line
(1) JQ500 concrete mixer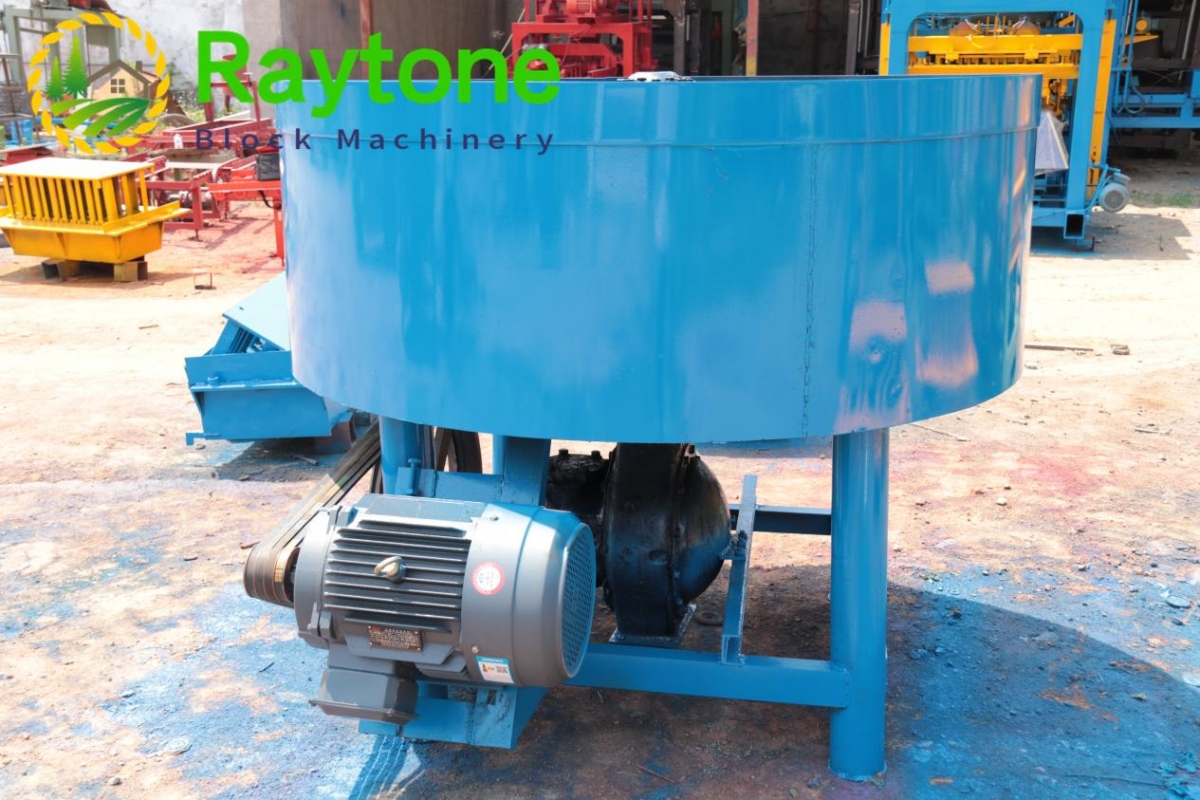
Diameter: | 1.5 M |
Input capacity: | 800L |
Output capacity: | 500L |
Productivity: | 20 cubic meters per hour |
Power: | 11KW |
weight | 500KG |
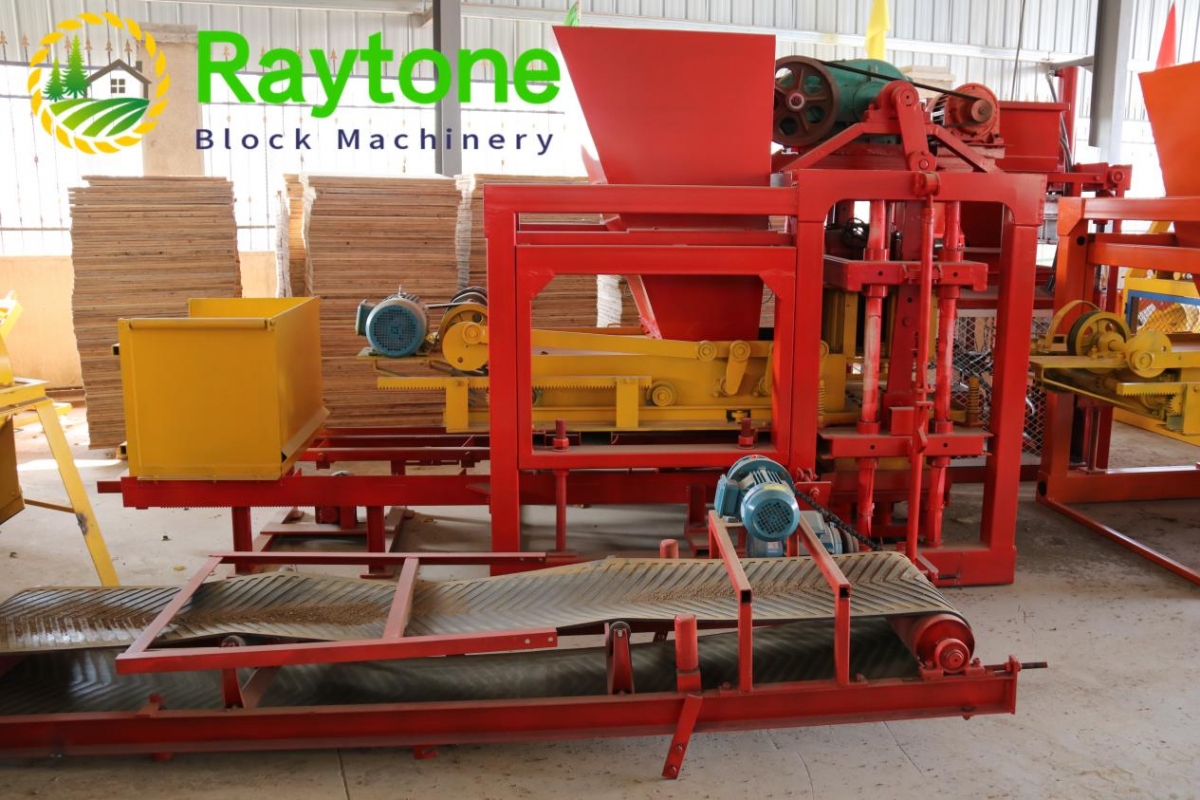
length | 6M |
Power | 1.5KW |
weight | 300KG |
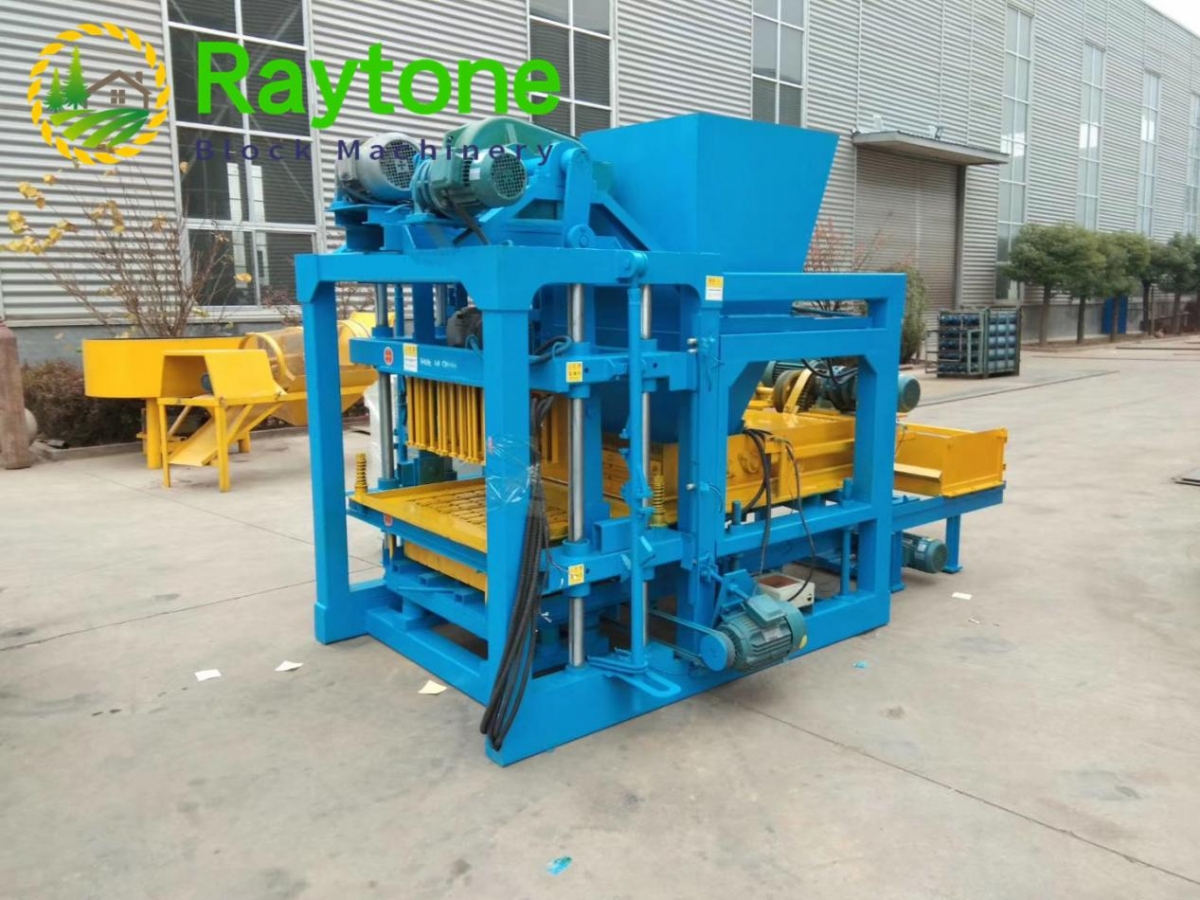
Model | QT4-25 automatic block machine |
Power: | 18.6KW |
Vibration method: | Platform vibration |
Pallet size | 880*550*22mm |
Weight: | 4000kg |
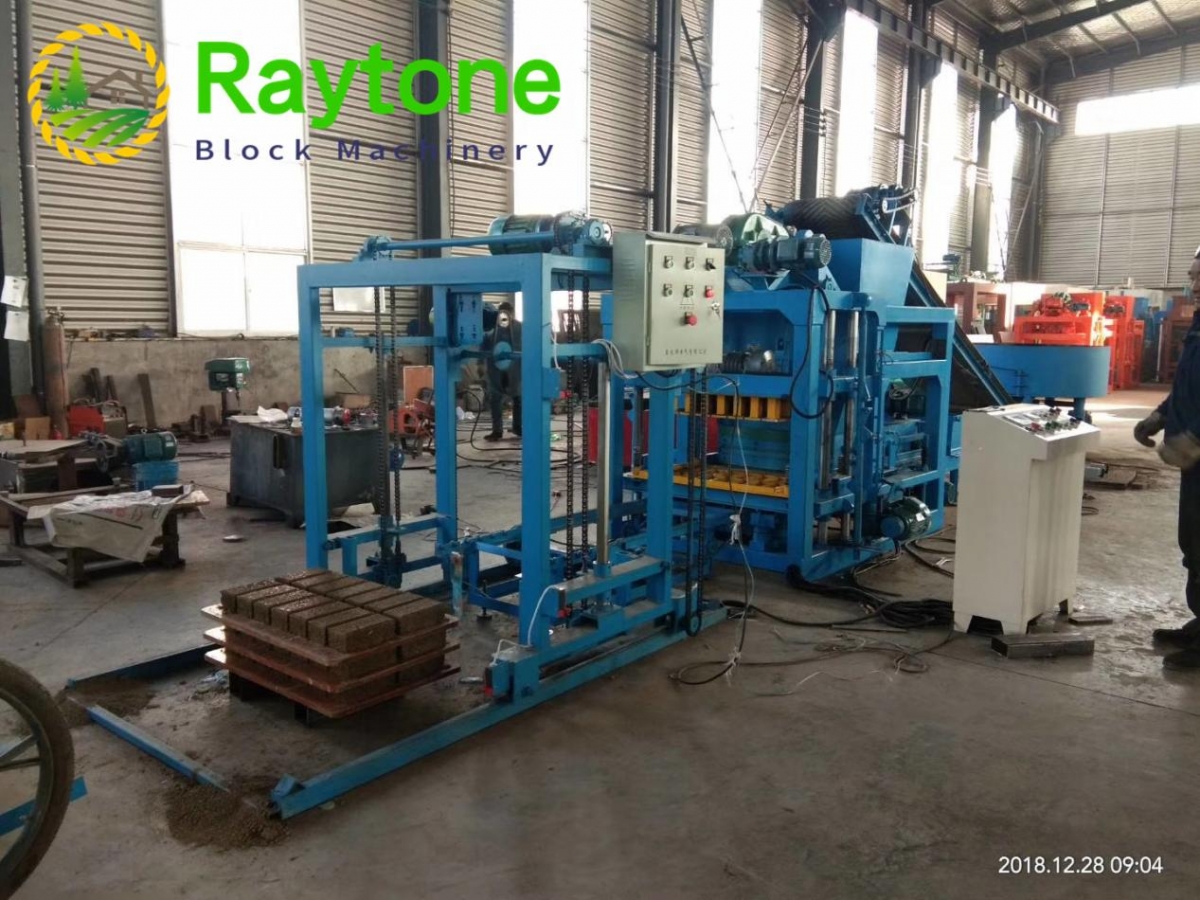
Power: | 3.0KW |
Weight: | 500KG |
Application: | Stack finished blocks one layer by one layer |
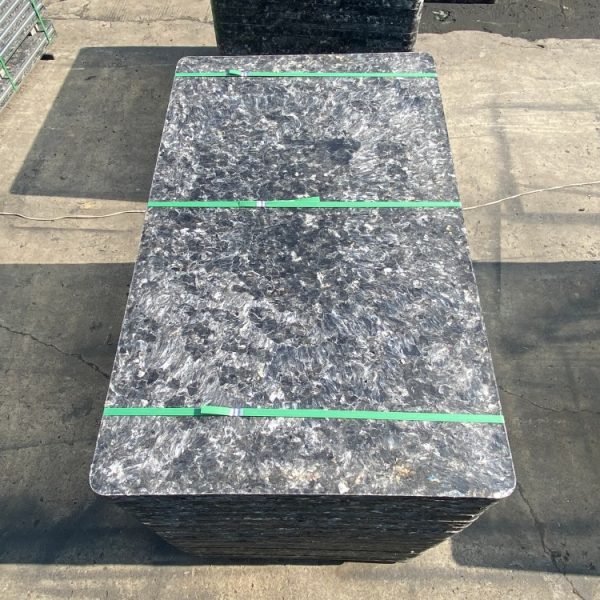
size | 880*550*22mm |
Weight: | 12.8kg /piece |
life | 8 years |
Daily productivity of QT4-25 Automatic Block Machine
3. Packing list for QT4-25 Automatic Cement Block Machine
1 | JQ500 Pan Mixer | 1 set | 6 | Block conveyor Machine | 1 set |
2 | 6M Belt Conveyor | 1 set | 7 | Blocks Stacking Machines | 1 set |
3 | Brick Pallet Feeder | 1 set | 8 | Manual trolleys | 2 set |
4 | QT4-25 Host Brick Machine | 1 set | 9 | GMT brick pallet | 1000 pieces |
5 | PLC control Panel | 1 set | 10 | Spare parts | 1 set |
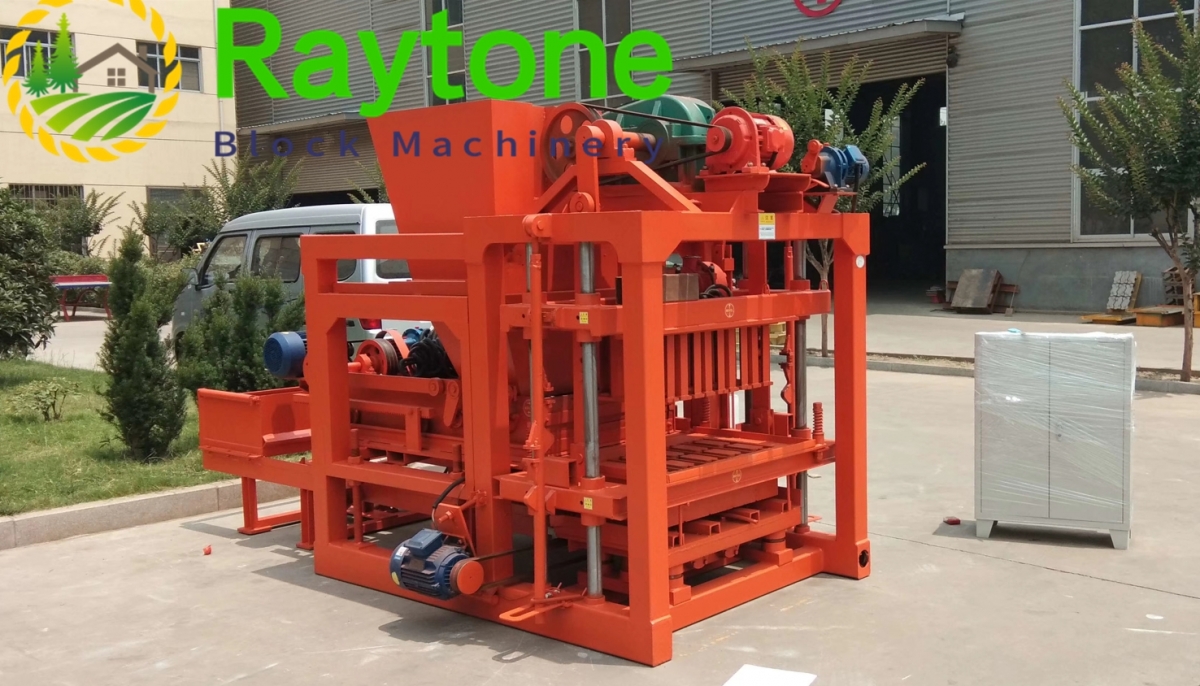
4. Shipping and Packing
We can package the machines according to your requirements. Whether it’s a plywood box or an iron frame, we can use either. Each machine will be wrapped in plastic film to reduce wear and tear. Our on-time delivery rate is 100%.
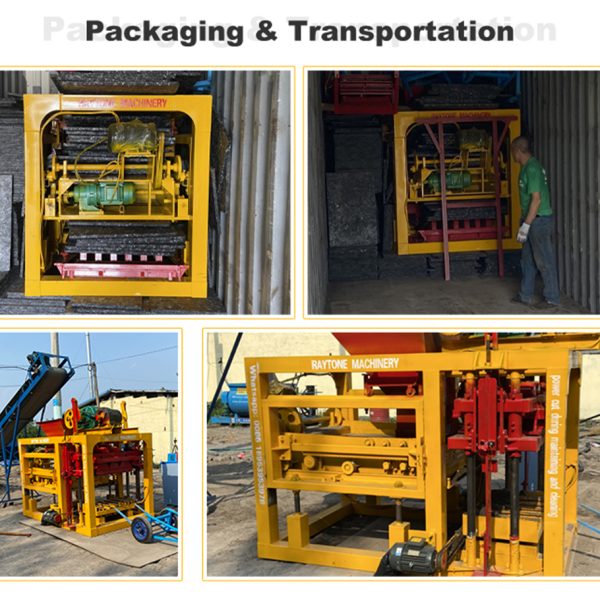