Line Basic requirements for start-up:
the following information for the QT10-15 automatic brick making machine is theoretically for reference, the real site production data may be small different as per different raw materials etc.
The factory area takes into account the raw material placement area, machine placement area, finished product area, drying area, etc., and requires about 2500-6500 square meters.
land area |
2500-6500 Square Meters |
Water Consumption |
12 T/day |
Workshop area |
200 Square Meters |
Electricity Voltage &Frequency |
220V/380V/415V; 50HZ/60HZ |
Labors Quantity |
6 workers |
Power Consumption |
125.2KW*8 Hours=1001.2 KWH; |
Cement Consumption |
31.5 Tons per day |
Sand consumption |
126 tons per day |
|
|
Crushed stones consumption |
156 tons per day |
(1)The QT10-15 and QT12-15 Automatic brick making machine are all big capacity block making machine models,
so their each single machines are almost same except the host brick machine.
Their first same sections are list out, which can refer to the following link for details:
①Raw materials storage section: cement silo and cement screwing machine for QT10-15 Automatic brick machine
Function: the 100 tons cement silo is used to store the bulk cement, if the client doesn’t have bulk cement locally, cannot use this cement silo, so it is an optional;
The 8 Meters length cement screwing machine is used to screw the cement from cement silo to the cement scale, which is installed on the JS750 concrete mixer;
The cement screwing machine is also an optional equipment, which is together with the cement silo.
② Concrete mixing stage: PLD1200 three-bin mixer, used in QT10-15 automatic brick-making machine.
The PLD1200 concrete mixer has two functions: one is to store raw materials, and the other is to weigh different types of raw materials; this ensures the accurate composition ratio of the concrete blocks and maintains the stability of the concrete block quality.
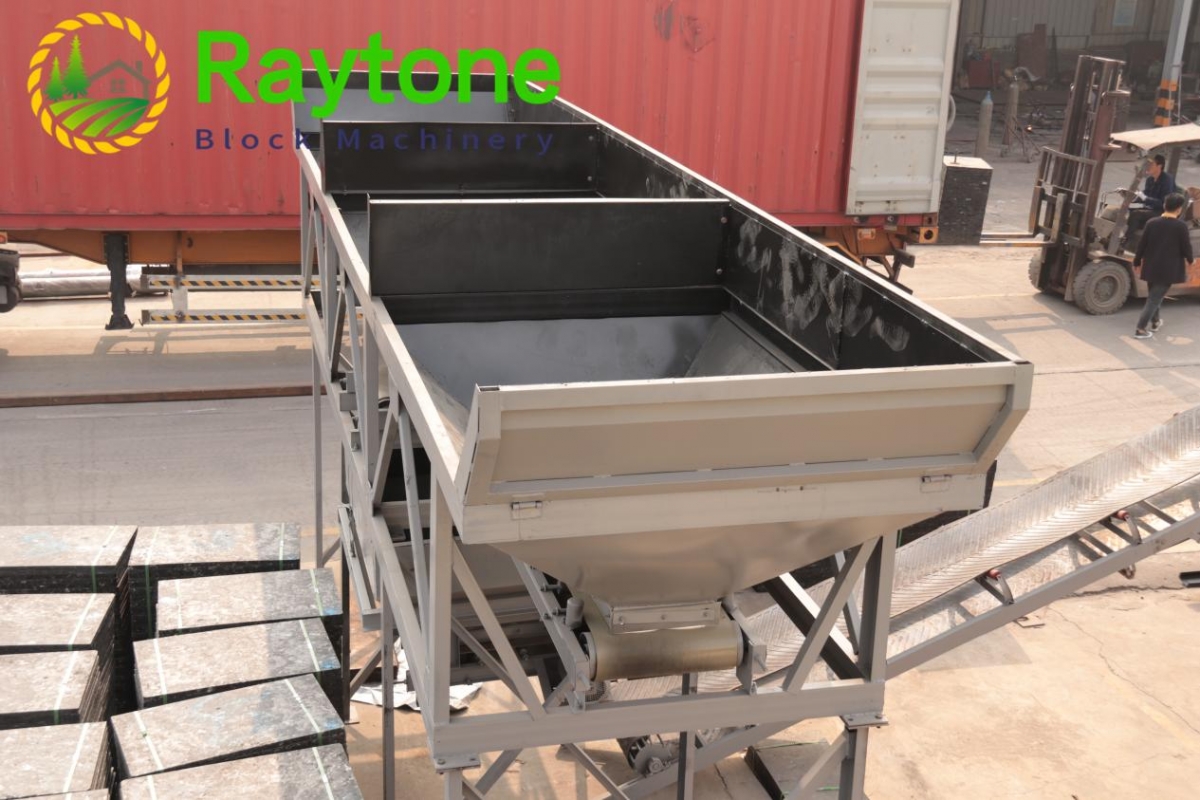
③ Concrete mixing section: JS750 twin shaft concrete mixer and cement scale for QT10-15 Automatic brick machine
There are two models of JS750 concrete mixer, one is with elevator hopper, the other one is without elevator hopper, the JS750 concrete mixer without elevator is using fast belt conveying machine to feed raw materials into the mixer;
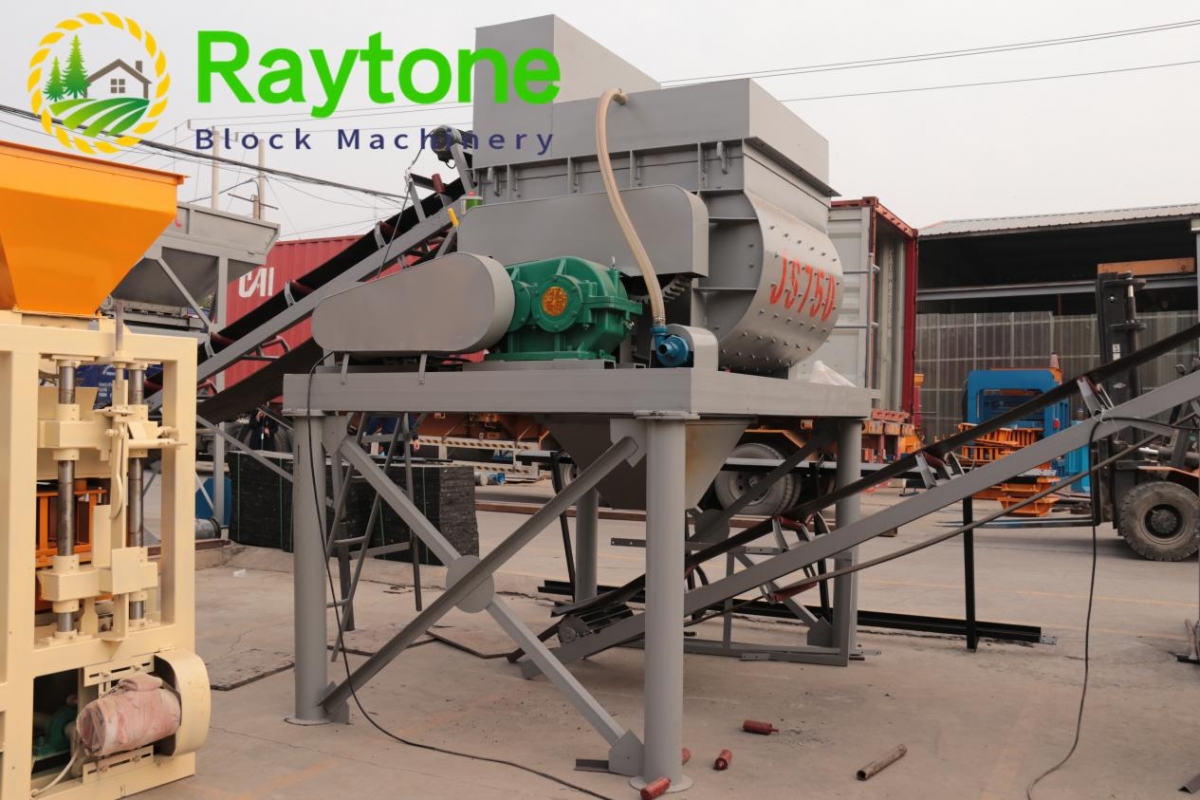
④
Hydraulic station, this is to supply the hydraulic oil for cylinders of QT10-15 automatic brick making machine; the cooling water pump is installed on, which can cool the hydraulic oil to let hydraulic station work normally.
⑤
PLC control panel for QT10-15 Automatic brick machine
PLC is an advanced microcomputer system, Automatic fault diagnosis, procedure is interlocked, can ensure every motion of the machine fluently and in high efficiency. The Siemens Brand PLC control panel can be supplied as customized. Our self-owned brand PLC is using Schneider and China top brand electronic elements, also have a reliable performance and low fault rate. The setting of every machine motion can be done via the touch screen, nice human-machine communicating.
⑥
paver brick surface coloring section: to give paver brick surface color
⑦
automatic stacking machine: used to stack the produced blocks, ready for transport to curing area.
⑧
brick pallet loading machine for QT10-15 Automatic brick machine, to supply the brick pallet to the block machine pallet feeding machine, can save labor.
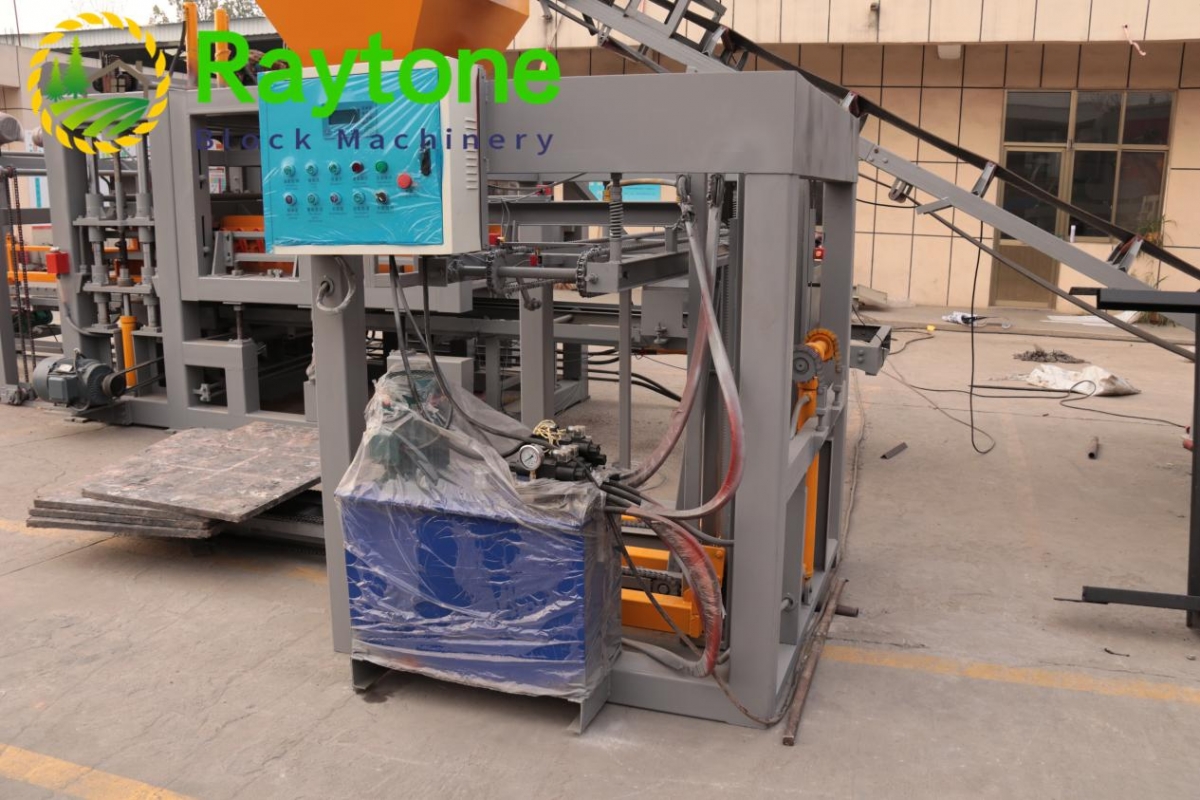
⑨
GMT brick pallet, please refer to this link of GMT brick Pallet. The QT10-15 automatic brick making machine brick pallet size is 1100*900*30mm , while QT12-15 automatic brick making machine is using 1400*900*30mm size brick pallet;
⑩ brick moulds for QT10-15 Automatic brick making machine
900 degrees celsius high temperature heat treatment carburizing heat treatment makes the mould much more strong and durability, longer life.Cutting uses wire cutting to make the mold standard in shape and accurate in size. After heat treatment and carburizing technology, the rigid molecular structure is changed, the strength and hardness are increased, and it is more wear-resistant. After positioning processing and milling machine technology, the surface of the mold is smooth and smooth, and the dimensions are more accurate. The mould can be used around 100 thousand times.
(2) QT10-15 Host brick making machine introduction
Motor power:
Vibration motor power: 11KW*2 (client can also choose to use 4 pieces of 5.5KW vibrating motors)
Hydraulic Station motor power: 22KW
Raw materials discharging motor: 2.2KW
Raw materials distributing motor: 4KW
Host block machine total power: 50.2 KW
QT10-15 host brick making machine main technical parameters |
(1) |
Dimension of host machine |
9400*2860*2980mm |
(7) |
water Consumption |
12T/day |
(2) |
Weight of the host machine |
9.8T |
(8) |
Voltage |
customized |
(3) |
Moulding period |
12-20S |
(9) |
Total required machine power |
103.3 |
(4) |
pallet size |
1100*900*30mm |
(10) |
Diesel Generator capacity |
120KVA |
(5) |
Vibration force |
120KN |
(11) |
workshop area |
250-300 m2 |
(6) |
labour |
5 to 7 |
(12) |
Land Area |
2500-6500 m2 |
The QT10-15 automatic brick making machine Adopts more advanced material-feeding technology,material from the hopper fall into the mould case rapidly and evenly,
make the weight error less than ±5%,the intensity error less than≤±15%.